Key Benefits
1. Less Weight
3D printing can manufacture strong but lightweight structures that achieve weight reductions of around 40-60% or more. This results in leaner cost structures, material savings and lower fuel consumption.
2. Functional Integration
The 3DP process allows maximum functionality to be integrated into as few parts as possible. The advantages are (i) Assembly and quality assurance costs are reduced and (ii) Vulnerabilities associated with assemblies of many different components are eliminated.
3. Complex Parts
3D printing enables a wide range of design optimizations from part customization and upgrades to exclusive innovations that can only be manufactured additively.
4. Significant Cost Reductions
Additive manufacturing is a tool-free process. This means that significant cost savings can be achieved in comparison to conventional manufacturing processes. The additive manufacturing is tool-free process and complexity – for-free process
5. Lower CO2 Emissions
A more efficient engine and/or turbine and lightweight parts for interiors reduce fuel consumption and hence the CO2 emissions of an aircraft.
6. Flexible Production Planning
The tool-free production process allows product adaptations to be implemented more quickly. Spare part storage can be significantly reduced by manufacturing on-demand without extended lead time. The cost advantages become very apparent over the long life-cycles of the aircraft.
Applications
Jigs & Fixtures
Big benefits exist for some of the more mundane 3D printing applications, including jigs and fixtures making. For each aircraft, companies have 3D printed hundreds of fixtures, guides, templates and gauges 3D printed, generally with 60 to 90 percent reduction in cost and lead time compared to other manufacturing processes.
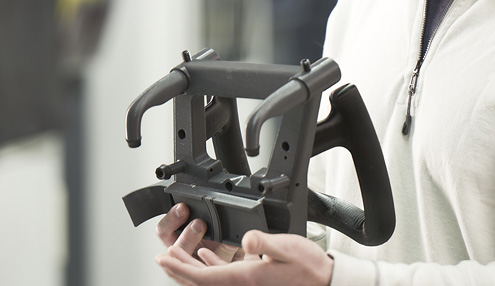

Surrogates
Surrogates are placeholder parts used throughout a production process that represent components that are later installed in final assemblies. Surrogates are mainly used for training. NASA and several air force bases commonly use surrogate parts on the production floor.
Mounting brackets
3D printing is commonly used to manufacture structural, low-volume metal brackets (with DMLS/SLM) that mount complex life-saving systems to the interior wall of a plane.
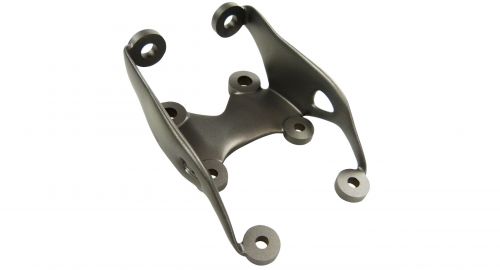
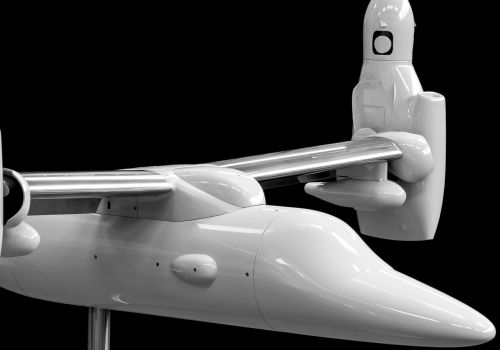
High detail visual prototypes
3D printing is also ideal for aerodynamic testing and analysis, as the surface finish that can be achieved is often representative of a final part. 3D printing is used routinely to manufacture aerospace components that rely on aesthetics over function, such as door handles and light housings to control wheels and full interior dashboard designs. 3D printing with Material Jetting can produce multi color designs with a surface finish comparable to injection molding. These visually appealing models allow designers to get a greater understanding of the form and fit of a part before production decisions.
Aircraft Interiors
Designing and manufacturing for aircraft interiors hinges on weight reduction. To reduce weight, cutting down on material is key. 3D printing allows for the creation of continuous units, meaning all necessary features are consolidated into one part thereby reducing material usage, additional hardware and attachment features, and overall weight. Interior Aircraft components such as air ducts, wall panels, seat framework, headlights prototypes, doors, console control part and dashboard interfaces have all benefited from the ability to create complex geometries and organic shapes for reduced weight with 3D printing. As more and more airlines seek to add seats or increase passenger space, 3D printing offers a way to simplify parts and thin down panels, overhead compartments and seat components.
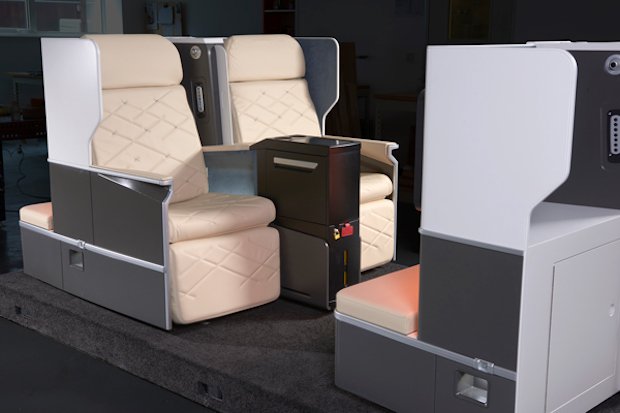