Key Benefits
1. Design Communication
3D printed models allow design intention to be communicated and showcase the overall form (and at times, the fit and function) of a concept.
2. Design Validation
There is a 3D Printing technology suited to every prototyping need, with some 3D Printing engineering materials also allowing for full testing and validation of prototype performance.
3. Pre-production
One of the areas 3D Printing has been most disruptive in is the production of low-cost rapid tooling for injection molding, thermoforming and jigs and fixtures. This mitigates the risk when investing in high-cost tooling at the production stage.
4. Production
3D Printing is now a viable solution for many small and medium-sized production runs, particularly for higher-end automobile manufacturers or limited edition automobile designs that restrict production numbers to just hundreds or thousands, much lower than the typical average of millions.
5. Customization and R&D
AM has also allowed part consolidation and optimized the topography of many custom automotive components. Parts can be tailored to a specific vehicle (custom, lightweight suspension arms) or driver (helmet or seat) and in some cases, performance enhanced to provide a more superior user experience.
Applications
Bellows
3D Printing (specifically SLS) can be used to make semi-functional bellow pieces where some flexibility is required in assembly or mating. Generally, this process is best considered for applications where the part is exposed to very few repetitive flexing motions. For projects that require significant flexing, other Polyethylene based SLS materials such as Duraform “Flex” are better suited.
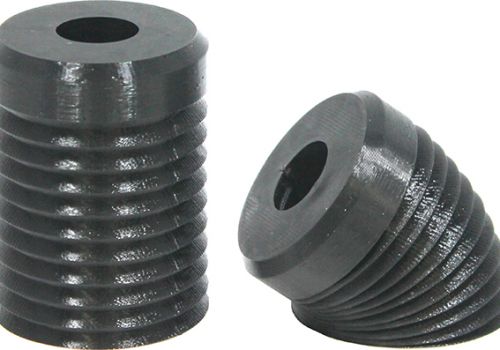

Complex Ducting
By using 3d printing to manufacture non-structural low volume ducting such as environmental control system (ECS) ducting for aerospace and performance racing, you can design highly optimized, very complex single-piece structures. With 3DP, it is possible to engineer in variable wall thicknesses and increase the strength-to-weight ratio through the application of structurally optimized surface webbing. This is a very costly detail to apply with a traditional manufacturing process.
High detail visual prototypes
Prototypes to demonstrate form (and at times, fit and function) can be quickly made at lower cost than traditional manufacturing processes. Depending on the technology used, a high level of detail can be captured through this process. In fact, prototyping is the single widely used application of 3d printing not just in the automotive industry but across most other industries as well.
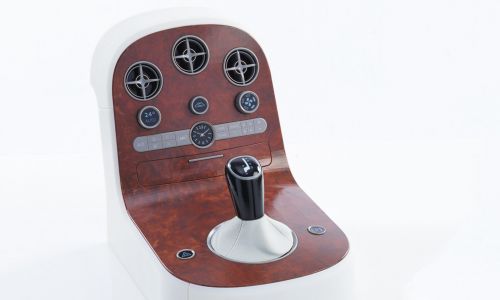
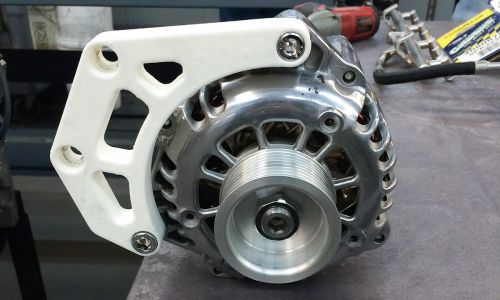
Functional mounting brackets
Being able to rapidly manufacture a complex, lightweight bracket overnight is a trademark of the 3D Printing industry. Not only does AM allow for organic shapes and designs to be manufactured but AM also requires very little input from an operator meaning that engineers can quickly take a design from a computer to assembly in a very short amount of time. This is not possible with traditional manufacturing techniques like CNC machining where a highly skilled machine operator is needed to produce parts. Powder Bed Fusion (PBF) technologies like SLS and DMLS/BMD (metal printing) are best suited for functional parts and offer a range of materials (from PA12 and nylon to titanium, stainless steel and inconel).
Jigs and fixtures
Jigs, fixtures and other tools utilized in manufacturing can be the backbone of a production floor. Successful repeatability, reliability and quality often rely on simple manufacturing aids that provide guidance and security during crucial assembly and inspection operations. Jigs and fixtures can be off-the-shelf, but often manufacturers will custom design their manufacturing aids for unique operations to their products. 3D Printing eliminates the cost, lead time and design barriers to adopting manufacturing aids on the shop floor. Thanks to its unique advantages over traditional manufacturing, 3D Printing can deploy jigs and fixtures where they previously could not exist.
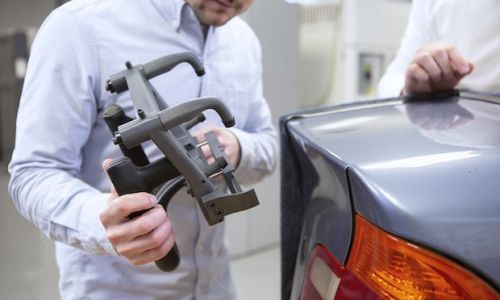
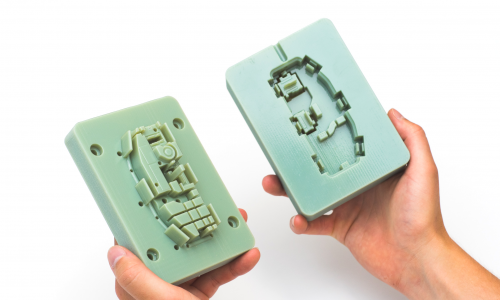
Short-run injection molds
For low-run molding, wear resistance is no longer the most critical factor. Certain 3D printing technologies such as Material Jetting and SLA can produce parts to high accuracy with excellent surface finish. When this is coupled with the modern temperature-resistant 3D printing materials and the design freedom that 3D printing enables, 3D printed molds are now a viable option for manufacturing low-run injection molding dies. 3D printed molds also allow the quick verification of the mold design, mitigating the financial risk of investing in an expensive metal mold.
Lightweight structures
Car manufacturers are always looking for new ways to reduce their product’s weight. Indeed, a lighter car consumes less fuel, which makes it more environmentally friendly. To do so, you can optimize the design of your parts. You can either create lighter structures thanks to innovative design patterns such as lattices or reduce the number of parts of the car thanks to a more integrated and inclusive design of the components within a sub-assembly.
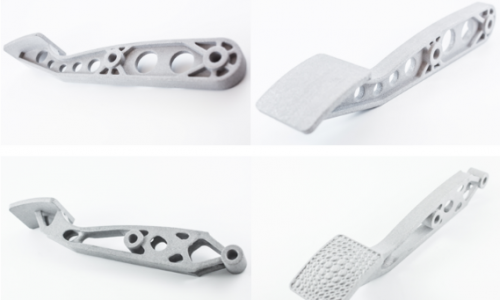