Key Benefits
1. Improving healthcare
The medical industry is a field in which innovation and new technologies have a direct impact on improving processes, operation results and saving lives. In the medical field, 3D printing enables doctors to work faster, shorten patient theatre time and improve operation results. The outlook for medical uses of 3D printing is evolving at an extremely quick pace as specialists are beginning to utilize the technology in more advanced ways. Patients are now experiencing improved quality of care through 3D printed implants and prosthetics.
2. Complex Operations
3D printing plays an important role in training future doctors and preparing for actual surgeries. 2D images are useful, however, they provide little visualization and do not represent actual human anatomy. 3D printing on the other hand, provides models that look realistic and mimic actual human anatomy. This makes the surgical process more accurate and effective.
3. Advanced technology
Future doctors can practice mocks surgeries on 3D printed organs. This is much more accurate than, for example, training on animal organs. Training on human-like, 3D printed organs increases the quality of skill-sets that the doctors obtain during training and thus ensuing better medical treatment of patients.
4. Intricate care
3D printers create low-cost prosthetics where people need them, for example in war-torn countries. They are an affordable solution for people who cannot afford to buy a prosthetic. Low-cost medical equipment is also important in poverty-stricken countries and remote areas. There are areas where road infrastructure is too poor to deliver medical equipment on-time. 3D printing makes it easier to print the necessary equipment in those villages without having to regularly transport them.
5. Expensive procedures and long waiting time
3D printing allows manufacture of medical and lab equipment. It is possible to 3D print plastic parts of the equipment. This drastically reduces costs and time spent waiting to receive a new medical device from external suppliers. Furthermore, the manufacturing process and further applications are also easier. This makes equipment more readily available and allows low-income or hard-to-access areas to get 3D printed medical equipment more easily.
6. Customization
Making prosthetics the traditional way is very expensive because they have to be personalized to the individual. 3D printers give users the freedom to choose, e.g. different designs, forms, sizes and colors of their prostheses. This makes every 3D printed piece personalized. 3D printers also allow prosthetics to be more widely available at a lower price.
Applications
Bioprinting tissues and organoids
One of the many types of 3D printing that is used in the medical device field is bioprinting. Rather than printing using plastic or metal, bioprinters use a computer-guided pipette to layer living cells, referred to as bio-ink, on top of one another to create artificial living tissue in a laboratory. These tissue constructs are organised and can be used for medical research as they mimic organs on a miniature scale. They are also being trialled as cheaper alternatives to human organ transplants.
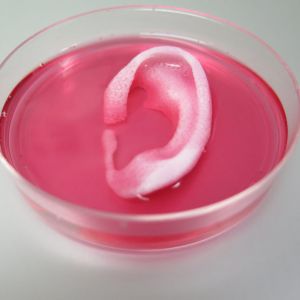
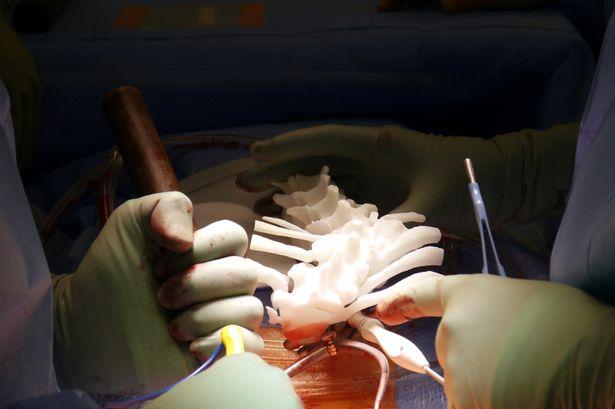
Surgery preparation assisted by the use of 3D printed models.
3D printing in the medical field is creating patient-specific organ replicas that surgeons can use to practice before performing complicated surgeries. This technique has been proven to speed up procedures and minimize trauma for patients. This type of procedure has been performed successfully in surgeries ranging from a full-face transplant to spinal procedures and is quickly becoming a routine practice in advanced economies.
3D printing of surgical instruments
Sterile surgical instruments, such as forceps, hemostats, scalpel handles and clamps can be produced using 3D printers. Not only does 3D printing produce sterile tools, but some are also based on the ancient Japanese practice of origami, meaning they are precise and can be made very small. These instruments can be used to operate on tiny areas without causing unnecessary damage to the patient. One of the main benefits of using 3D printing rather than traditional manufacturing methods to produce surgical instruments is that the production costs are significantly lower.
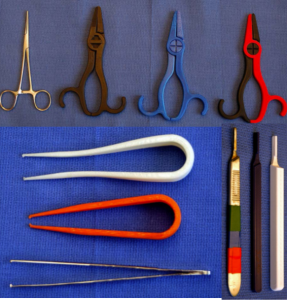
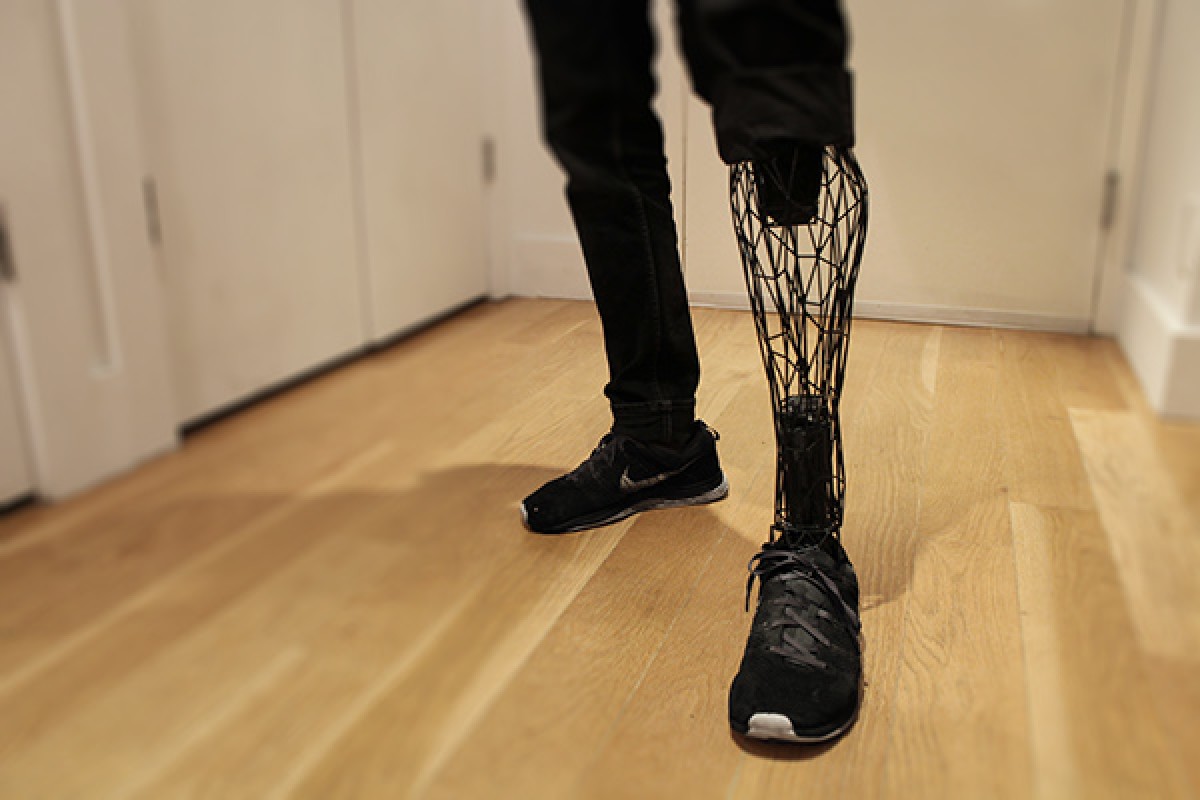
Custom-made prosthetics using 3D printing
3D printing in the medical field can be used to produce prosthetic limbs that are customized to suit and fit the wearer. It is common for amputees to wait weeks or months to receive prosthetics through the traditional route; however, 3D printing significantly speeds up the process, as well as creating much cheaper products that offer patients the same functionality as traditionally manufactured prosthetics.
The lower price point of these products makes them particularly applicable for use with children, who quickly outgrow their prosthetic limbs.
Patient-Specific Devices and Implants
Prosthetic medicine is not the only medical field that requires a high degree of customization. Patient-specific devices (like hearing aids) and implants (like artificial joints, cranial plates and even heart valves) are rapidly converting to 3D printing for its easy customization and fast production.
Heart valves and hearing aids have traditionally required a full week of extensive, handmade adjustments by skilled workers. Before 3D printing, producing a hearing aid took nine steps from casting to fitting. Now, hearing aids can be 3D scanned and printed in a single day.
There are design advantages, too: 3D printed silicone heart valves provide an exact fit that rigid, traditionally manufactured heart valves simply can’t. For implants like titanium artificial joints or cranial plates, 3D printing can create complex, porous surfaces that make patients’ bodies less likely to reject the implants.
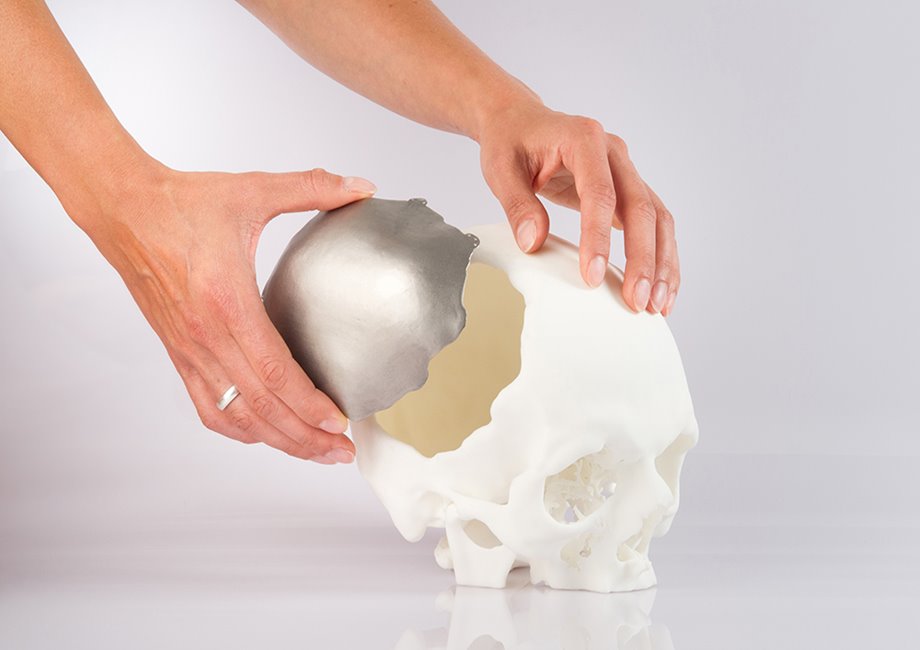
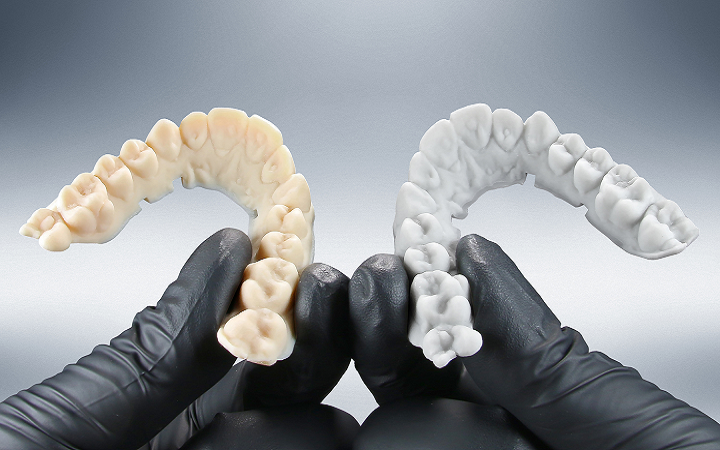
Dentistry and Orthodontics
Like prostheses, dental implants and orthodontic devices require extensive customization with a high degree of accuracy. We rely on our teeth to stand up to heavy use day after day—as a result, dentures, crowns, implants and retainers need to be durable, precise and comfortable. On top of that, they need to be made of biocompatible materials like cobalt chrome and porcelain.
3D printing allows dental and orthodontic professionals to accomplish all of this faster and at less cost than traditional methods like machining. A combination of 3D scans and x-rays can be used to produce high-quality dental devices without any casting or setup time.
Even for devices like braces or expanders that do not require 3D printed components, 3D printed models made from sterilizable plastics can be used to measure form and fit, eliminating the need for lengthy patient fittings or multiple visits to the doctor’s office.
Customizable Drugs
One area of 3D printing that holds exciting promise is personalized medicine. As new drugs are developed that have increased potency and differential effects within populations, there is a need to consider new manufacturing methods and novel supply chains to realize the paradigm of personalized medicines. 3D printing offers the possibility of creating a personalized medicine system through automated control over drug dose and is suitable for both low and high drug concentrations.
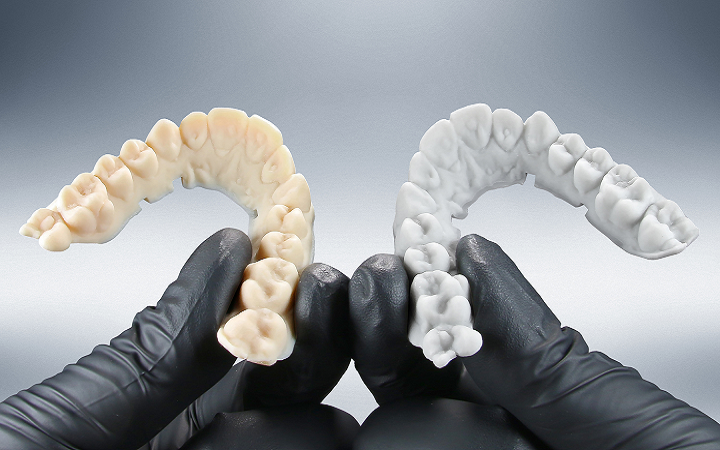