The company
Medicare GmbH is a company founded in 1993 that provides a variety of technical aids. At their now nine sites in Mecklenburg-Vorpommern, Medicare GmbH offers their customers services in the area of orthopaedic technology, rehabilitation technology, shoe technology, health care supply stores and home care. The best possible quality of care, a friendly and comprehensive service and a complete supply provided from one source are their main priorities.
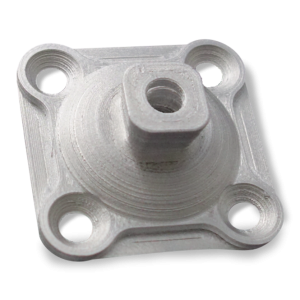
Challenge
Since the beginning of 2017, Medicare GmbH has been dealing with the topic of additive manufacturing in the area of orthopaedic technology. The aim is to find an alternative for the production of prostheses and orthoses as well as connected components such as prosthesis adapters.In this context, the foremost priorities of our concern are quality, cost, competitiveness, the enhancement of the value chain within the company and eventually the implementation of a new manufacturing method.
This case study considers a prosthesis adapter*1 with the following properties:
- socket adapter with adjustment core, adjusting holes 5 mm
- material:aluminium, stainless steel or titanium
- weight:aluminium: 50 g, titanium: 50 g, stainless steel: 50 g
- load class*2: aluminium 100 kg, titanium 175 kg, stainless steel 150 kg
Currently, the components are produced externally. The purchase price lies between 30 and 60 euros (net), depending on the material.
Advantages of the ExAM 255
The ExAM 255 is the world‘s first industrial 3D printer which uses the CEM process to produce metal parts. This is not its only unique selling point though.The ExAM 255 offers the possibility to print products made of metals, ceramics, plastics and reinforced plastics by using standard injection molding pellets – without the need of expensive adaptations to the machine.
Compared to typical FFF printers, the ExAM 255 offers a faster build rate and a larger choice of material. The printer is able to reach printing speeds of up to 150 mm/s and has two print heads.
Market comparison
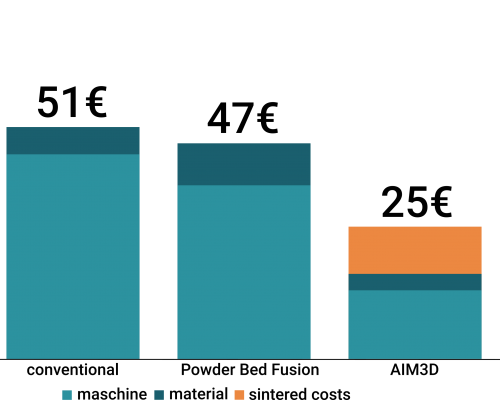
Saving of cost
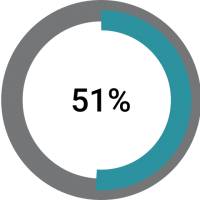
Saving of time
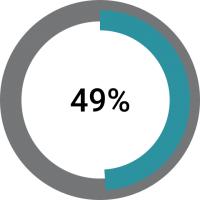
Solution
For Medicare GmbH it is of special importance to be able to quickly produce custom-fit products for their customers. The numbers in this case clearly speak for a production with the ExAM 255: the costs can be reduced by 54% and the production time can be reduced by 49%.Medicare is now able to develop each piece individually.Adjustments based on customer requirements regarding wear comfort and wear time can thus be considerably optimized.Based on the good cooperation and the clear advantages for both companies, Medicare and AIM3D will continue their joint efforts to revolutionize the market of orthopaedic technology, rehabilitation technology and shoe technology and develop further application examples.