UNA wheel is a unique electric drive that can turn a wheelchair for disabled people into a self-propelled device and give extra freedom to every user by expanding the range they can cover.
The primary challenge faced by our customer was to concentrate the fabrication of individual functional parts (for instance, electric drive fixture) on its own site and to eliminate the risks of failure to observe quality and fabrication dates when ordering parts from outside contractors. The simplest solution is to fabricate the fixture from steel tubes by laser cutting and welding. However it is time-consuming and expensive to fabricate this part in a small run.
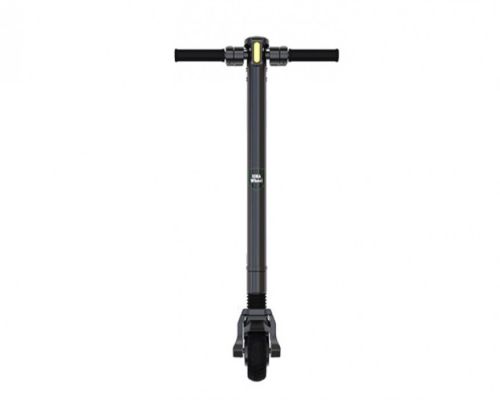
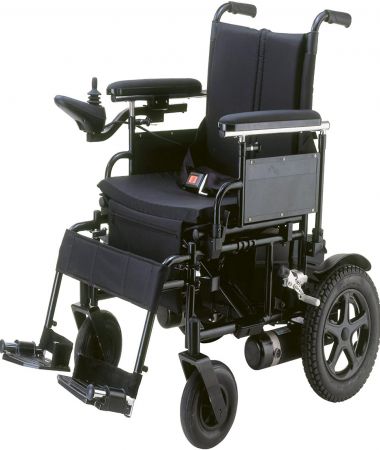
Supreme Motors team started to look for alternate solutions. Option 1 is 3D-printing of the part on FDM-printer made of high-duty Ultem plastic (PEI, polyetherimide). This solution made the part 5 times lighter, less costly, and, most importantly, enabled fabrication of small runs using in-house resources. However, the fixture did not prove to be durable enough and failed the stress tests.
An alternate solution was anisoprinting on Composer A4 additive machine. PETG was used as the primary reinforcing material. The part withstood a 117 kg dynamic load on a cobblestone road, in off-road conditions, and on the crossings of tram tracks and other obstacles typical for urban environments. Overall structural strength was confirmed by tests under critical loads: hits of the electric console by wheel from a height of 40–50cm.
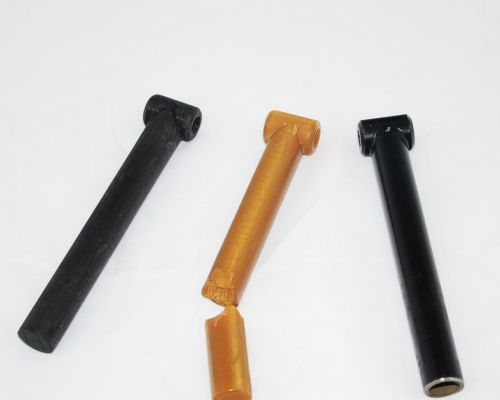
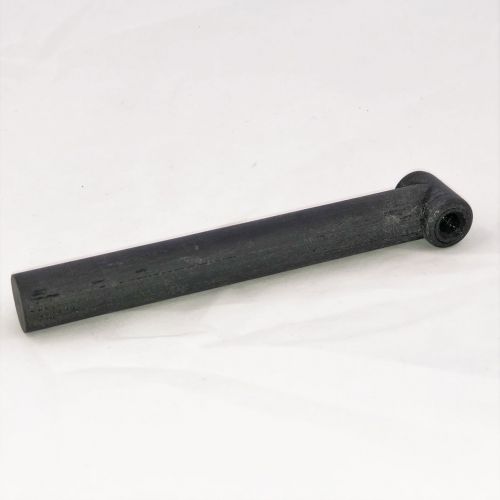
Nikolay Yudin, founder of Supreme Motors:
“THE COMPOSER PRINTS UNIQUE PARTS! 7.3 TIMES LIGHTER WHILE PRESERVING THE FUNCTIONS ON OUR PROTOTYPE PART. ULTEM FAILED WE WANT TO PRINT LONG PARTS COMBINED WITH NYLON”
Anisoprinting enabled UNA wheel to concentrate the fabrication of small-batch fixtures in-house. Light, durable, and functional component that has fully replaced a traditional metal part.