Key Benefits
1. Faster product development
Additive manufacturing significantly speeds up the design process since it requires no tooling. In contrast, traditional manufacturing can take months to produce the necessary tools to create end parts and prototypes. The defense industry can therefore take advantage of the technology to bypass costly and time-consuming tooling, thereby reducing the time required for product development.
2. Freedom of design
The defense industry can also capitalize on the ability of 3D printing to produce free form, optimized objects. This means that the weight of a part can be significantly reduced using additive manufacturing, saving material costs and production time. Leveraging advanced design tools, design engineers can reduce the number of components in an assembly to just one, and thus greatly simplify the assembly process.
3. Customized equipment
Not only does 3D printing allow for more design freedom, but it also offers the opportunity to create customized parts, tailored for specific functions. Rather than carry parts and pieces for all possible configurations, soldiers can use 3D printing systems to manufacture parts on demand. For example, researchers in the US Army can now 3D print customized drone air frames tailored to the specific needs of a given mission. Customizable 3D printable designs are therefore vital to achieving greater levels of agility and flexibility within the military.
4. Localized and on-demand production
Coordinating logistics and transportation makes up a significant part of any military budget. For an industry that spends billions of dollars on logistics alone, it may prove to be more cost-effective to print custom parts, tools and spare parts near the point of use – a solution that additive manufacturing provides. This could mean that soldiers in remote areas can also use 3D printing to their advantage.
Applications
Structural components for defense systems
The first fighter jet with 3D printed components onboard took flight in 2013, and since then, it’s clear that additive manufacturing can make a significant impact in the production of end parts for military equipment. The defense industry is currently investigating the capabilities of direct additive manufacturing even more extensively, as the technology can help reduce production costs while producing complex lightweight components in small volumes. The applications of additive manufacturing here vary, from complex brackets and small surveillance drones, to jet engine components and submarine hulls. In addition to this, 3D printed weapons like grenade launchers are already a reality, with missiles under development.
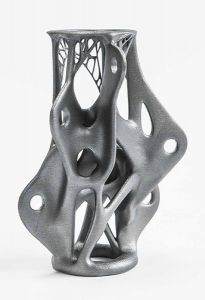

Replacement parts, tooling, and maintenance
As military equipment is typically kept and used over many years, the defense industry relies heavily on spares and replacement parts. For years, outsourcing has been the most common way to procure these parts, with thousands of replacement parts and tools for military equipment sourced from external companies. Here, additive manufacturing becomes a viable option, as it facilitates the cost-effective and relatively quick production of parts and tools on demand.
Modeling, test units, and prototyping
Additive manufacturing is an ideal solution for creating quick concept models and prototypes, and it is widely used in the defense industry to rapidly produce prototypes without the need for expensive tooling. Design concepts as well as validation testing can be done much faster, thereby shortening the product development cycle.
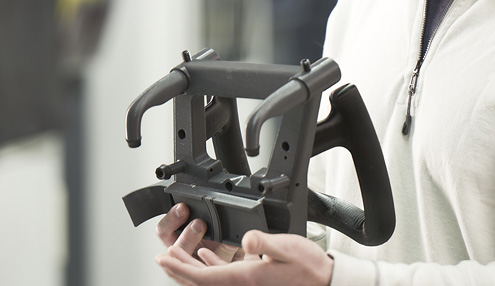